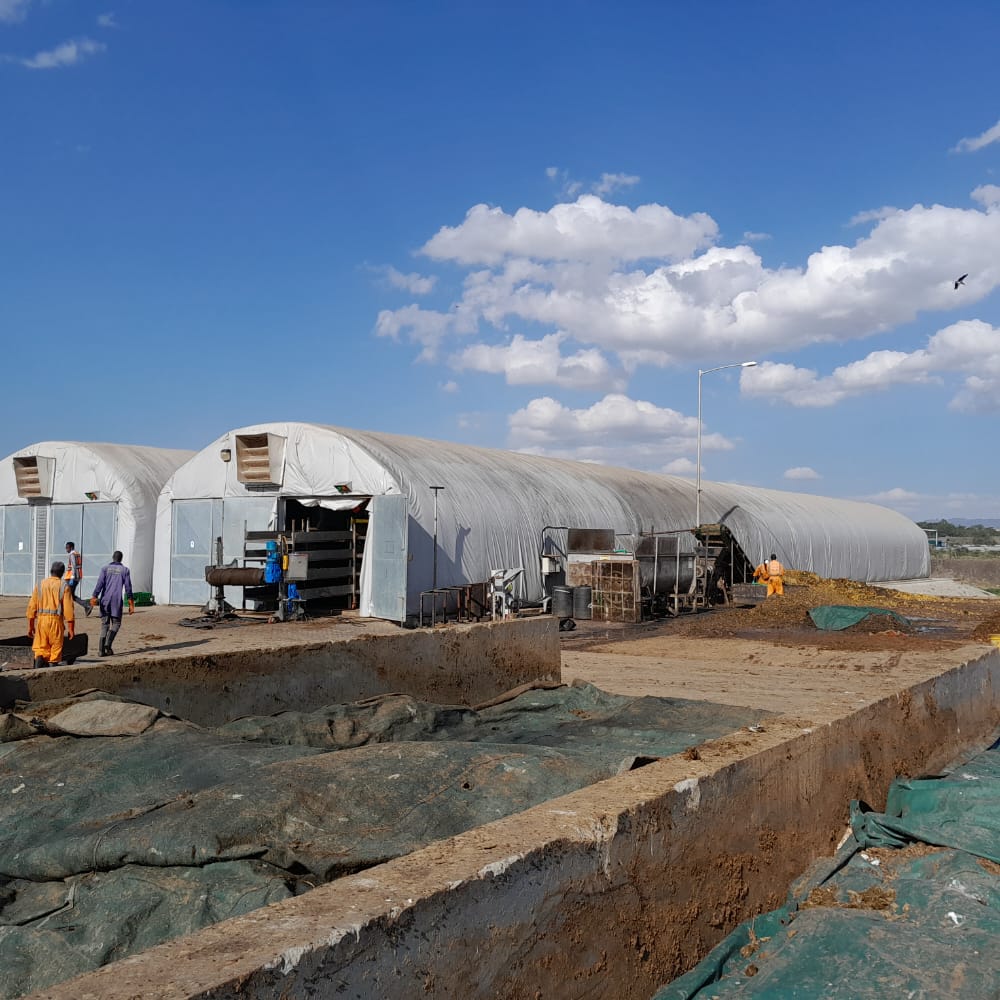
The E4C Fellowships, sponsored by Engineering for Change, empower early-career engineers and other technical professionals worldwide to work on local and global sustainable development challenges while building professional skills and relationships. The Autodesk Foundation supports up to 30 E4C Fellows, who will commit five months to working for portfolio organizations on Design for Good, Advancing Workflows, and Impact Research projects. E4C Fellows work remotely with flexible schedules during both summer and winter cohorts. This story is part of an ongoing series profiling several Autodesk Foundation-supported E4C Fellows.
The problem of dealing with organic human waste remains a taboo topic, as well as a deceptively pervasive challenge, according to Fresh Life (formerly known as The Sanergy Collaborative), an organization founded in 2010 to solve the waste sanitation crisis through the circular economy. Around half the world’s population lives in a place where human waste ends up in their environment, according to Fresh Life. That leads to the death of 2 million children a year, as well as damage to water systems, the environment at large, and the economy.
To combat this problem in a way that could reach everyone equitably, Fresh Life has developed a 3-step waste system that can complement water-based sewage systems. It includes toilets that contain waste safely, waste collection services, and safe upcycling that produces fertilizer, fuels, and animal feed.
It’s that final component of upcycling that has spurned a two-year relationship with the Engineering for Change E4C Fellowship program to work on optimizing black soldier fly (BSF) farming from greenhouses. BSF farming is one of the most popular types of insect farming because it feeds on organic waste and can output fertilizer and nutrient-rich feed for livestock.
Circulating air for the circular economy
BSF farming from greenhouses can make human sewage management sustainable and environmentally friendly by following the key tenant of a circular economy: turning what was seen as waste into a resource. BSF larvae feed on an organic waste substrate, and at the end of the cycle, farmers harvest the larvae and package them as a protein-rich feed for livestock and fish. This feed makes a sustainable alternative to other commonly used protein feed sources such as soy and fishmeal. After harvesting, the remaining organic residue is collected and composted to be packed and sold as organic fertilizer.
To maximize the production of BSF farms’ agricultural outputs, the flow of fresh air through the shelves holding BSF larvae has to be optimized to control CO2 and ammonia levels. Along with brainstorming ideas for greenhouse air-handling systems, Fresh Life’s 2021 E4C Summer Fellowship Program team used Autodesk Inventor to create CAD models of the greenhouse and its shelving units. It also began work on simulating the controlled environmental conditions of a greenhouse.
A second E4C Summer Fellowship in 2022 continued the project with mechanical engineer Isaac Charles Kimani as the Fellow. After graduating from Moi University in Kenya, Kimani immersed himself applying CAD, CAE, and computational fluid dynamics (CFD) tools to solve design and engineering problems in whatever project he was involved with.
As Kimani explains, airflow affects a greenhouse’s temperature, humidity, and aeration, all of which factor into the farm’s efficiency. Temperature (optimally 27-35OC) affects all of the larvae’s biochemical reactions that determine their growth and development. Low oxygen levels reduce larval activity, which in turn lowers the harvest weight, so proper aeration is important for maintaining the proper amount of oxygen. And finally, excessive humidity beyond the range of 70-75% leads to undesirable molding.
Kimani and his collaborators on the project set out to find areas for improvement in the BSF greenhouse aeration to achieve higher yields of protein feed and fertilizer. “Design is a collaborative effort,” Kimani says. “Different team members bring a different perspective and expertise. Effective communication is key to ensure everyone is on the same page.”
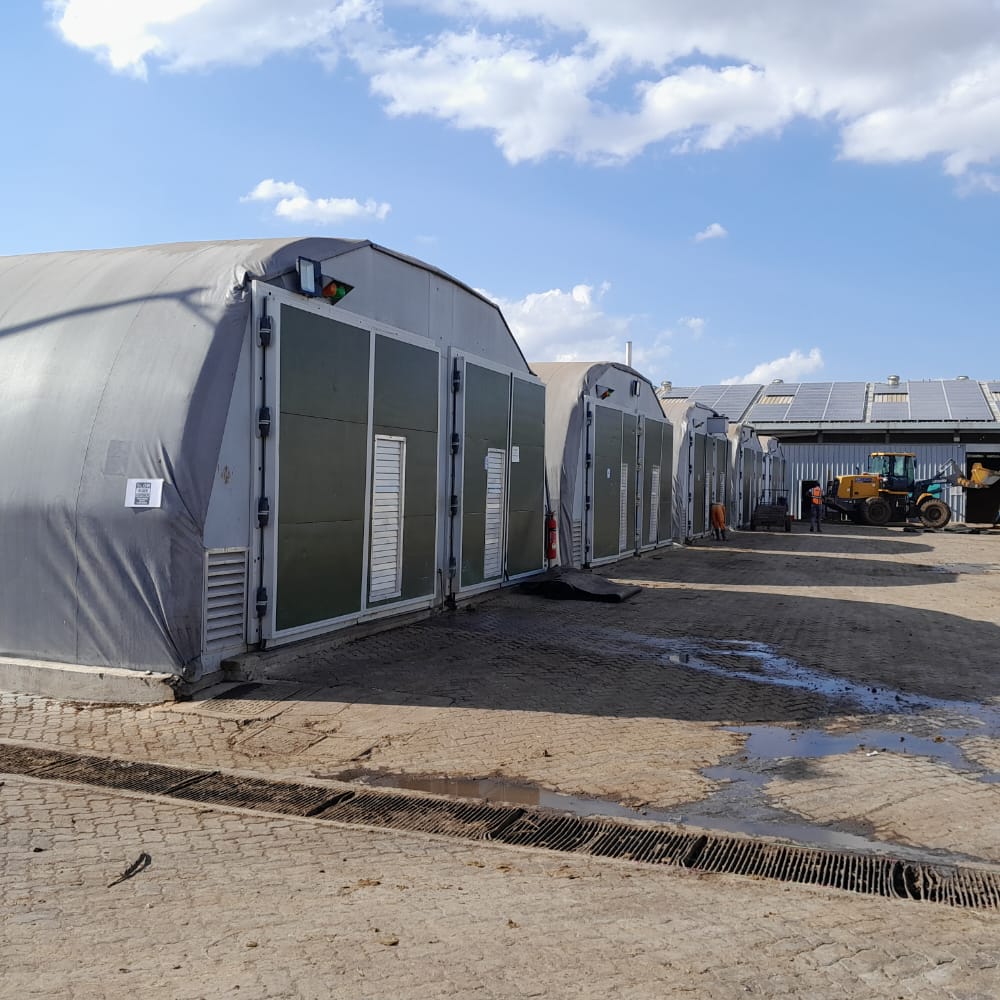
Simulation before fabrication
Using a cloud-connected platform like Autodesk Fusion 360 for the different BSF greenhouse and shelving CAD design concepts helped to keep Kimani and his colleagues aligned in their communication on a centralized, always up-to-date system. They also used Autodesk CFD, a software for simulating complex liquid, gas, and air systems, to evaluate and simulate the air flow and circulation inside the greenhouse.
Kimani says that this software made it possible for them to develop a digital twin of the BSF greenhouse respiration chamber to be used in the prototyping stage. They made the 3D models in Fusion 360, while simulating the real-world air-flow conditions of the chamber designs in Autodesk CFD. “The necessity to fabricate and physically test the different concepts was eliminated,” Kimani says, leading to significant time and cost savings.
After analyzing the performance of its design parameters in the software, the Fresh Life team selected the final design concepts to be incorporated into a BSF greenhouse. Kimani says the next step will be prototyping those designs to evaluate their respiration chamber’s performance as a fabricated product in physical space. Before too long, his design refinements could be improving BSF greenhouse farming’s yield for one of Fresh Life’s founding partners, Regen Organics, to turn into insect protein animal feed and regenerative organic fertilizer.
Learn more about the ongoing E4C winter and summer cohorts and how to apply for future projects.