Trial and error is especially costly in metal additive manufacturing. With so many variables across materials, machines, and part designs, it is almost impossible to know the formula for success.
Thermomechanical simulation, especially Netfabb’s multi-scale approach, provides a big advantage. Between 2012 and 2018, over $7.3M USD has been spent validating the Netfabb Simulation solver predictions by comparing them with the experimental results for materials, print parameters and design cases/geometries to help customers save time and money minimizing failures with metal additive manufacturing.
Part/Powder Interaction
Description: Two simulations are run to investigate the effect of including loose powder in an analysis. The first simulation does not model the loose powder and instead approximates energy lost by conduction into the powder as an artificial heat loss prescribed to the external surfaces of the geometry. The second simulation explicitly models the loose powder and the interaction between the parts and the powder through conduction.
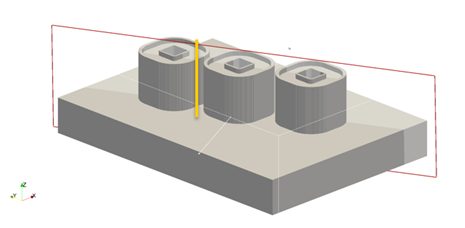
Figure 1: Experimental setup of the geometries. The line used to compare the model to the experiment is highlighted in yellow.
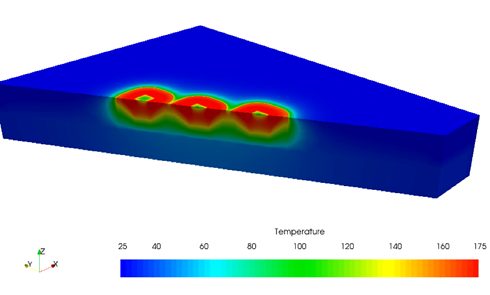
Figure 2: Thermal simulation results for the simulation case explicitly modeling the loose powder.
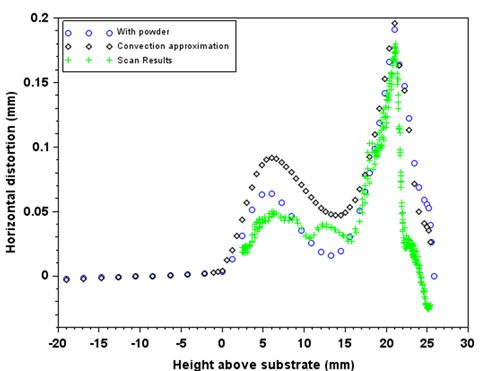
Figure 3: Simulated distortion results for the two cases compared with the experimental measurements. Experimental data courtesy of America Makes, GE GRC, and United Technologies Research Center.
Conclusions:
Explicitly modeling the loose powder and the interaction between parts results in much closer agreement with the experiment than the case assuming an artificial heat loss on the free surface of the geometries. In order to achieve accurate simulation results for cases such as this, it is necessary to model the full build plate including the loose powder.