Trial and error is especially costly in metal additive manufacturing. With so many variables across materials, machines, and part designs, it is almost impossible to know the formula for success.
Thermomechanical simulation, especially Netfabb’s multi-scale approach, provides a big advantage. Since 2012, over $7.3M USD has been spent validating the Netfabb Simulation solver predictions by comparing them with the experimental results for materials, print parameters and design cases/geometries to help customers save time and money minimizing failures with metal additive manufacturing.
Support Failure Prediction
Description: A component manufactured at the Penn State CIMP3D Additive Manufacturing center experienced a failure of the support structure. The experimental result was used to validate the support failure capability of Netfabb Simulation.
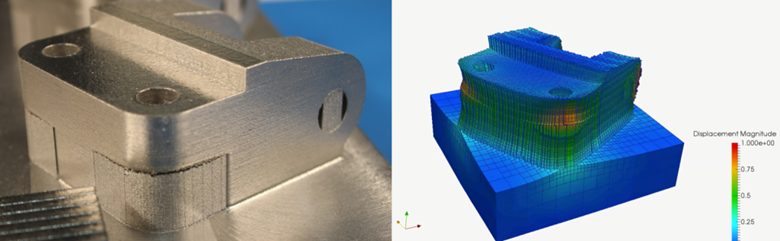
Experimental build showing support failure (left) and simulation results (distortion magnified 5x) showing support failure. Images courtesy of Dr. Ed Demeter (Penn State University).
Conclusions:
Netfabb Simulation is able to correctly indicate the region of support failure and simulate the delamination of the part from the support.