Authored By: Jeff Irwin, Principal Research Engineer, Autodesk
MPBF, which stands for metal powder bed fusion, is an additive technology accessible in Autodesk Fusion with the manufacturing extension and Netfabb Premium 2025. Using this tech, you can create an additive setup for supporting 3d printers, orient and arrange your parts, add support structures, and slice your models. Using Fusion or Netfabb, you can also create the additive toolpath and the machine build file, which control not only the toolpath but also important parameters such as laser speed, power, etc.
Many machine vendors have recommended settings depending on their printers and the type of metal you wish to 3d print, such as aluminum or titanium. However, it is also common practice for organizations to create custom settings to better suit their needs and produce better parts with minimized distortion due to high temperatures inherent in the metal 3d printing process.
One possible way to address the heat management problem is to delay the printing at each layer just enough so that the heat distribution in each layer is uniform. Another strategy is to modulate the power.
Autodesk Netfabb Local Simulation 2025 is software that can help with this challenge.
Power Modulation
The *TCTP
card, new in the 2025.0 release of Netfabb Local Simulation, modulates power in order to attain a constant interlayer temperature. Interlayer temperature is the temperature after the deposition and recoating of a layer, just before the next layer starts. This modulation feature iteratively repeats each layer of the thermal simulation and modulates the power until the resulting interlayer temperature is within a given tolerance of a target value.
The arguments of the *TCTP
card are shown below:
*TCTP
r1, i1, r2, r3, r4
r1: target interlayer temperature (°C)
i1: max iterations
r2: tolerance (°C)
r3: min power constraint (W)
r4: max power constraint (W)
Example
For example, to target a temperature of 100° C, these settings can be used:
*TCTP
# target, iter, tol, min pow, max pow (this line is a comment)
100.0 , 5 , 5.0, 0 , 2000
Figure 1 shows the interlayer temperature results with uniform 250 W power and with modulated power.
Figure 2 shows the optimized powers required to attain the uniform interlayer temperatures.
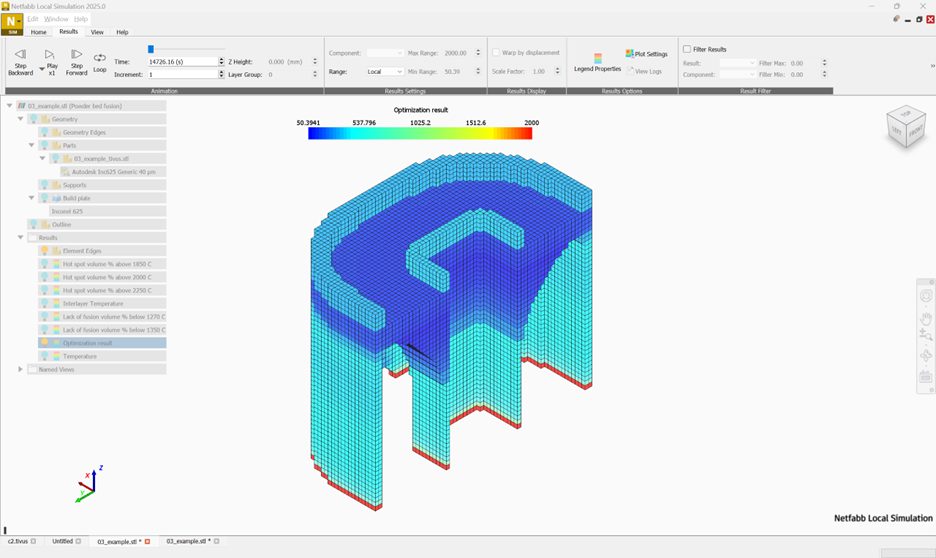
Figure 2: Optimized powers in Watts required to attain uniform interlayer temperatures.
Caveats
The optimized power results can be exported as an EnSight case file, a VTK file, and panzip file formats. Export to machine code is experimental. Please contact us if you would like to get more details.
Power modulation is intended for thermal simulations only. There is a coupling between power and the PRM kernel which is not accounted for if a single uniform PRM file is used for a whole part, so any mechanical analysis based on a *TCTP
thermal analysis will be inaccurate.