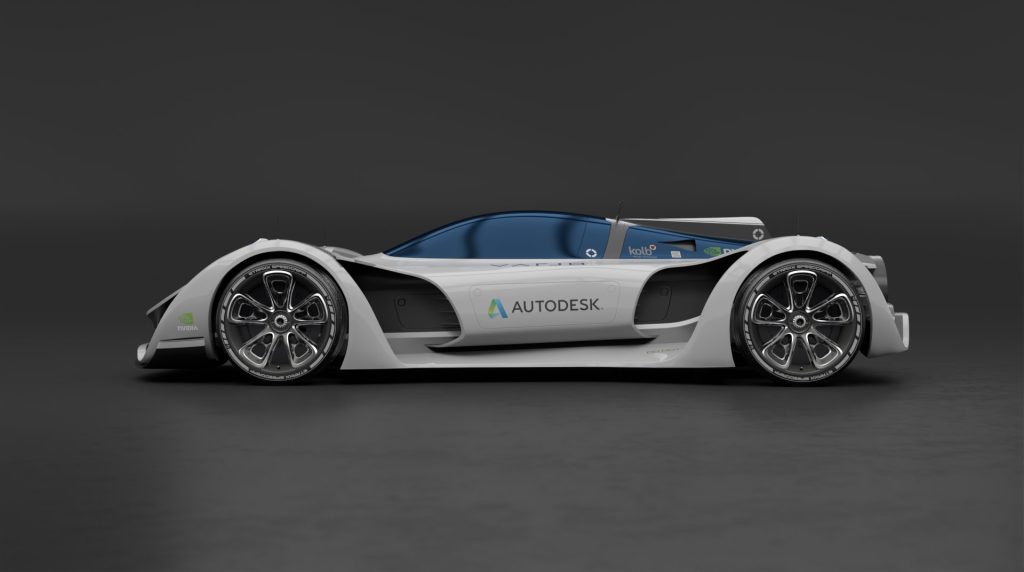
Florian Coenen, Technical Marketing Manager at Autodesk, created a car he called ETRAXX. We’ve been using it a lot here at Autodesk, so we wanted to share with you the process behind its creation.
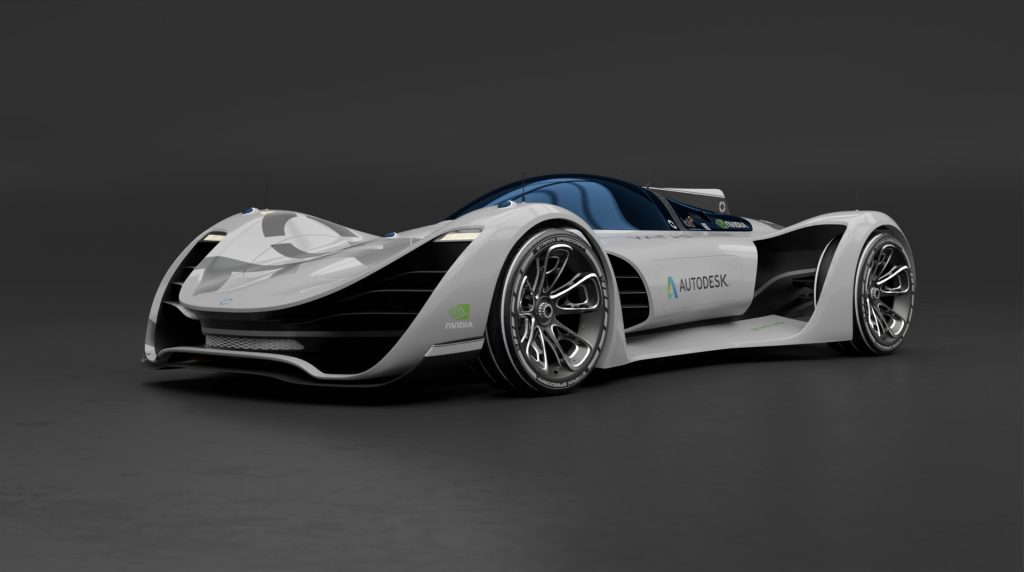
Its inspiration actually started with Alias 2021.3. This release had a number of new features – new SubD features for concept modeling, new Dynamo scripts, a new tire script, etc. Florian wanted to create a project that would let him go through a complete workflow and implement these new tools. Thus the start of the new ETRAXX shapes.
The new vehicle is a little bit Science Fiction and a little bit Formula One in a one-seater car.
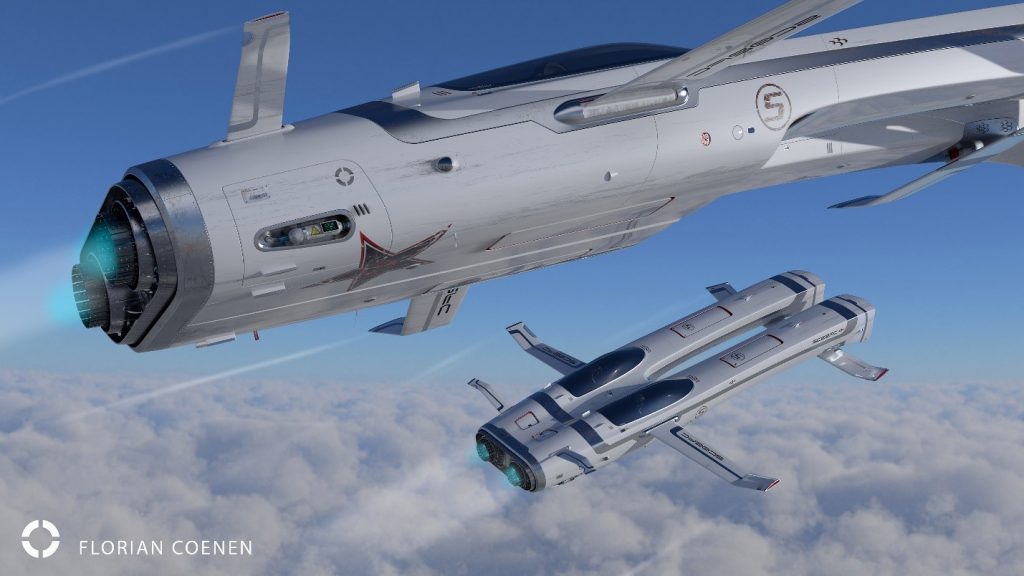
This project showcases a new tire script, which makes creating tires easier, letting you play with different sizes and styles.
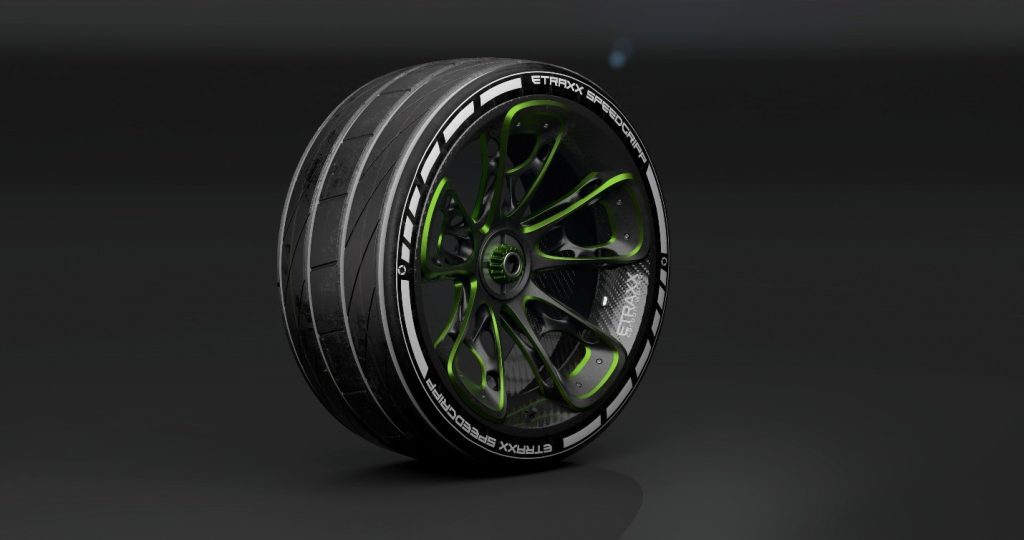
Florian also used a CFD calculation or simulation, that lets us see the air streams going into the car, into the wind tunnel, and out the back of the car.
One of the biggest design elements is a huge fan. (Yes, you read that correctly.) It might look like a turbine that gives you more speed, but it’s not. It’s actually an old technology, a fan designed into the car, that sucks the air from underneath the car, creating a little under-pressure (think: a Dyson on four wheels). Benefits: gives the car more downforce, omits the need for spoilers, makes a clean, closed shape.
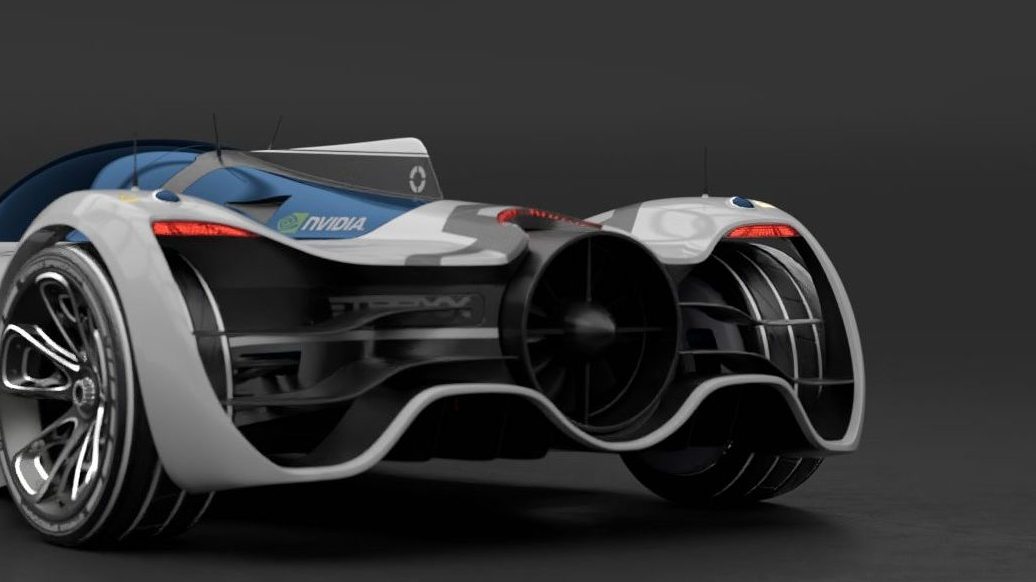
How does a project like this start? Inspiration and research (ideas, references, images, and photos). Then sketching gaffers on paper—proportions, and style. From there, create a photo of the sketch and import it into Sketchbook or Photoshop. Some digital editing, but the 2D image doesn’t need to be perfect at this stage.
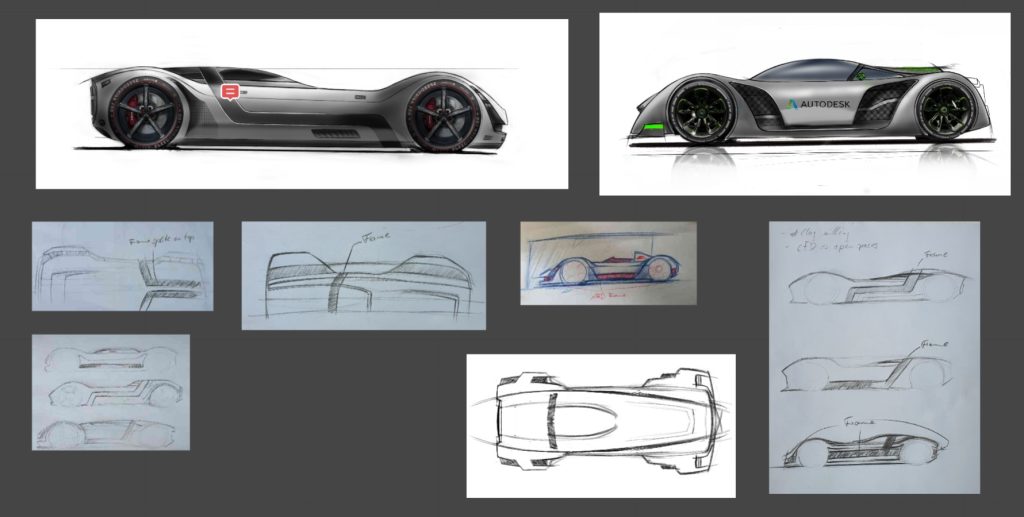
Florian then moves those rough sketches into Alias for concept modeling: SubD modeling, looking for the right proportions, concept surface flow, etc. The new hybrid modeling allows you to work with SubD and NURBS.
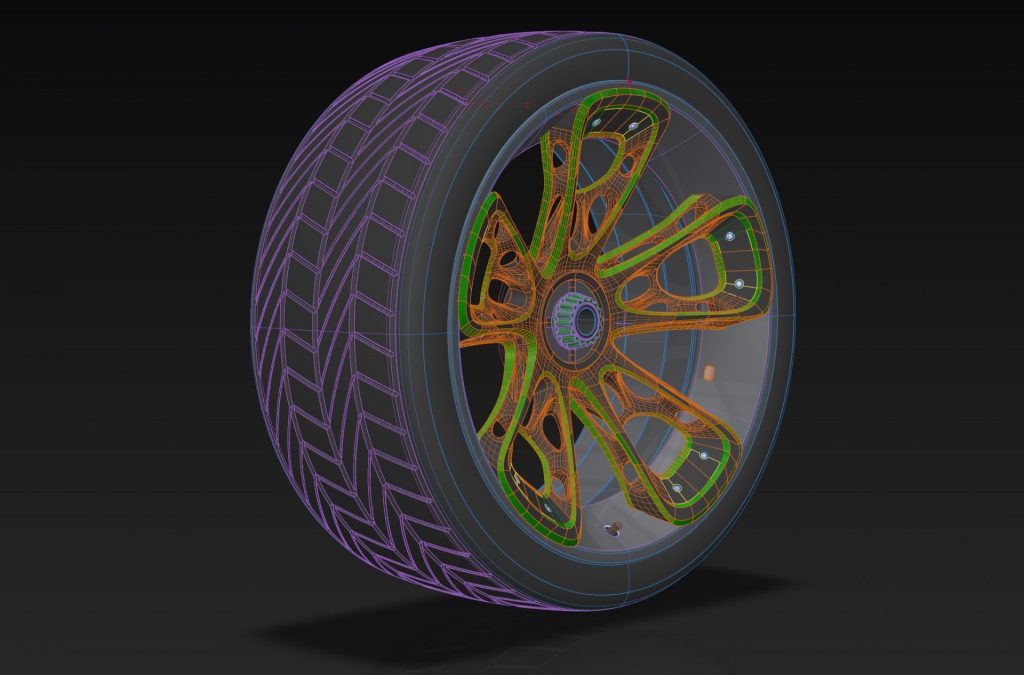
That leads right into the new implementations of working in VR, even at this early stage of the design process. You can explore proportions one-to-one, giving you much more confidence in your design process and speeding up decision-making.
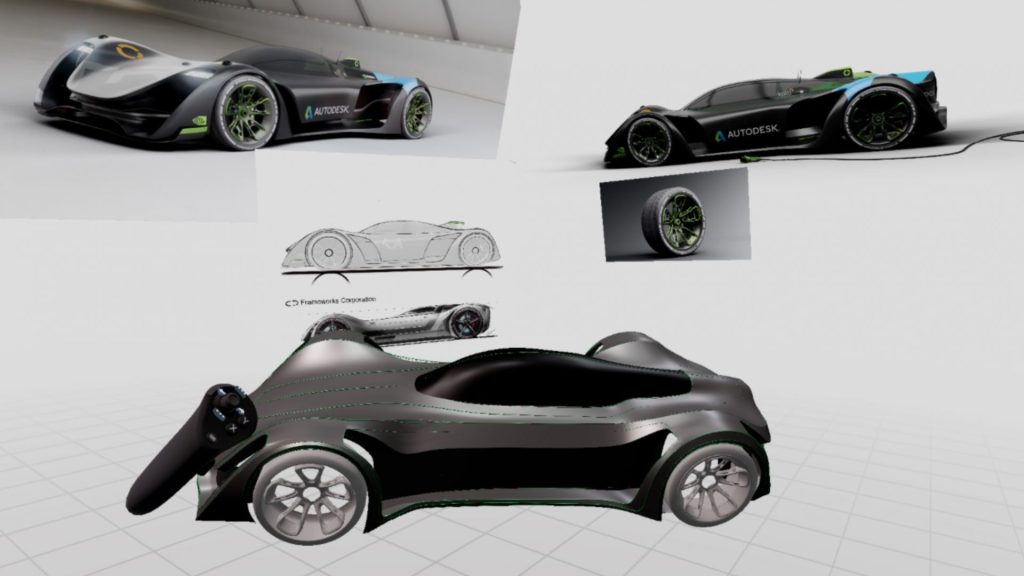
Stay tuned for the next episode, where we will go deeper into Alias, visualization, and VR design reviews
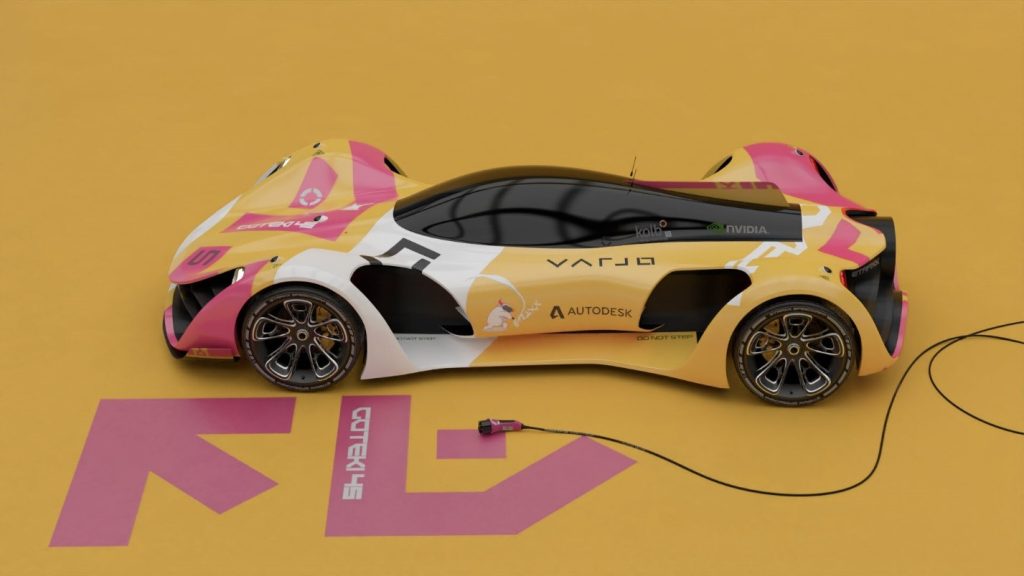