Autodesk Generative Design, Enhanced Simulation Tools Soon Available in Company’s Additive Manufacturing Software
By Greg Fallon, vice president of Simulation, Autodesk
Among comic book superheroes, Tony Stark is my favorite. Why? Because he doesn’t have powers from a freak accident or through an extraterrestrial birth. No, he’s an engineer who uses his brain – and technology – to solve problems. That’s what the capabilities in Netfabb 2018, our comprehensive additive manufacturing solution, will do for our customers: give them the power to combine human ingenuity and machine learning, where the two together are greater than the sum of their parts.
The first new service I want to talk about is Autodesk Generative Design – the technology that got me excited enough two years ago to become a part of this team. After a few years incubating as Project Dreamcatcher in our research group, and coming to life in projects with customers like Airbus and Under Armour, we are at long-last bringing our generative design solution to our mainstream customers.
Our CTO Jeff Kowalski calls generative design the true embodiment of CAD. Where for so much of its history, CAD software was more about computer-aided documentation, rather than computer-aided design, CAD packages took the designer’s direction and recorded the lines made by that designer. But with generative design, the computer helps generate design options for the designer’s specified goals. We’re on our way to having a true partner in our design software. Just as J.A.R.V.I.S. augments Tony Stark’s engineering genius, Autodesk Generative Design gives our customers superpowers.
So how does it work? Generative design technology takes goals set by a designer or engineer, e.g. size, weight, strength, style, materials, cost, and any number of other criteria, and then uses cloud computing to create a massive number of design solutions.
Using intelligent algorithms based on machine learning and advanced simulation, it produces smart design solutions that can be difficult for today’s designers and engineers to discover and model efficiently. The designer or engineer then identifies and adapts the right solution as desired. This process leads to major reductions in cost, development time, material consumption and product weight and gives our manufacturing customers the ability to design and engineer in brand new ways.
Autodesk Generative Design is not just topology or lattice optimization alone – it’s a massive step beyond that. While optimization focuses on refining a known solution without any notion of manufacturability, generative design helps the engineer explore a whole cadre of functional and manufacturing design options. With Autodesk Generative Design, a designer or engineer can not only discover a new solution, they can then bring it to life using additive manufacturing tools.
Stanley Black & Decker, the hardware and tool maker beloved by consumers and professionals alike, has recently seized on the superpower of generative design. The company’s newly-formed Breakthrough Innovation group started with a pilot project to make one of the tools an electrical line worker uses every day – a hydraulic crimper – better. In this case, better meant lighter. A conventional crimper weighs 15.4lbs and is used hundreds of times in a work shift. But this innovation team couldn’t just use lighter material—the tool still had to be just as strong and durable.
Frank DeSantis, Vice President of the Breakthrough Innovation group, worked with our consulting team to define the desired criteria and insert it into the Autodesk Generative Design service. After examining thousands of combinations of materials and processes, the service generated many options from which the innovation engineers were able to decide on a path forward, satisfied that they had explored all of the options – not just the three or four or even 10 options that engineers may have considered if they used traditional design tools.
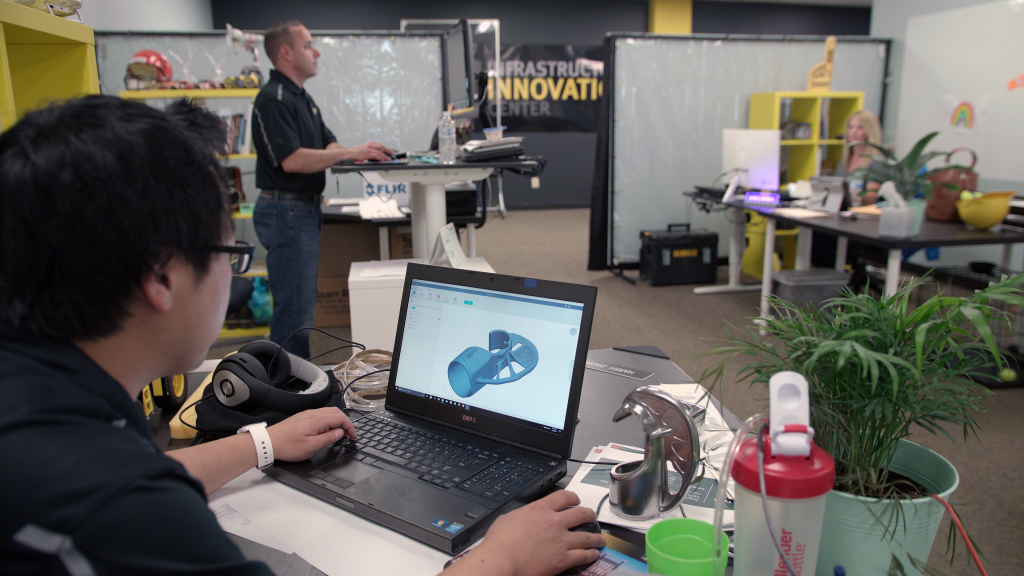
Harry Zhong, technical lead in the Stanley Black & Decker Breakthrough Innovation group, reviews concepts for the crimping tool attachment.
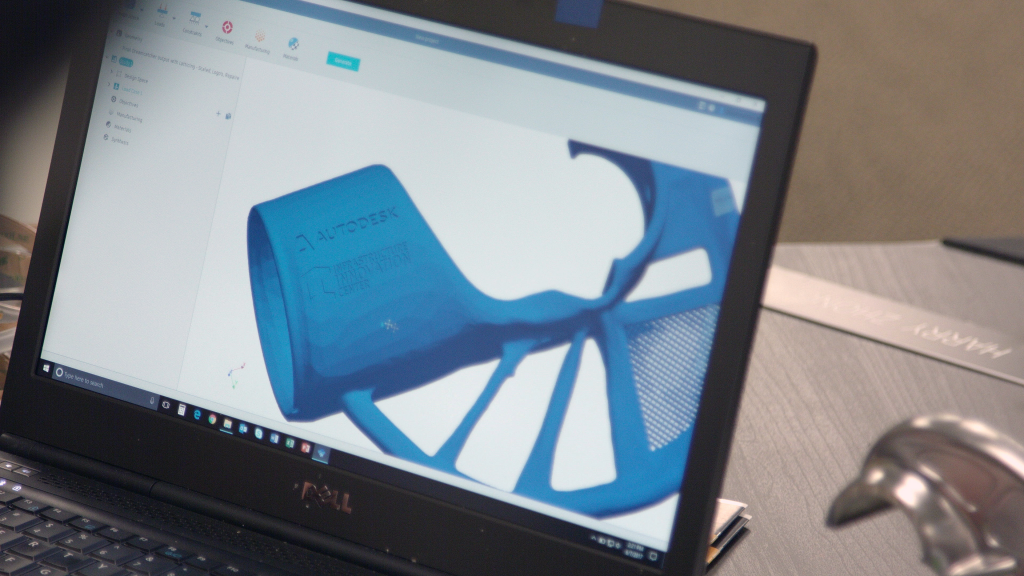
Generative design technology utilizes constraints input by the designer or engineer to create a massive number of design solutions.
The resulting generative design may look a bit unusual to some, but it reduced the hydraulic crimping attachment weight by just over 3lbs, or 60%. The simulations that were run concurrently showed that the tool maintained the strength characteristics of the original tool and, because the generative design service is available for Netfabb users, it also allowed them to create an additive manufacturing strategy to fabricate the new attachment.
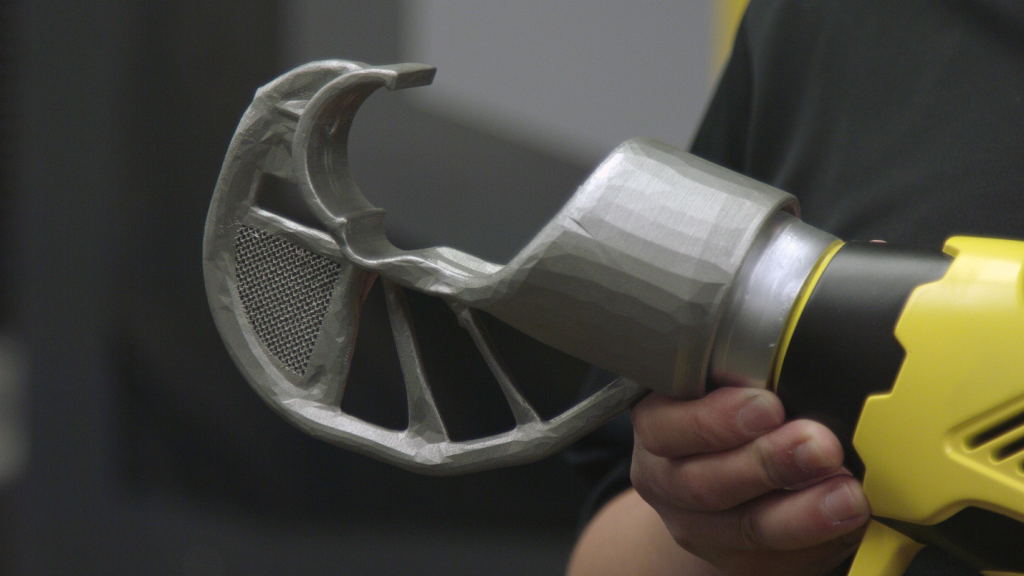
By using generative design and additive manufacturing technologies, the Breakthrough Innovation team was able to shave more than three pounds off the crimping tool attachment, reducing the weight by more than 60%.
When I asked Frank to describe his impression of the results, he echoed my sentiments in his own words:
“The generative design capabilities we can access with Netfabb are almost magical. It’s not brute force engineering. It’s elegant. You define a problem and you get a solution set unlike anything you’d predict. The results of the wire crimper project ensure we’re going to be applying the incredible combination of generative design and additive manufacturing that Netfabb offers to an array of other products we have in development. This is clearly the future and that’s what our Breakthrough Innovation group is all about.”
We didn’t just want to expand the innovative designs you can consider when solving complex problems, we wanted to give our users greater confidence in their ability to manufacture them. In Netfabb 2018, we’ve introduced the ability to predict and alter a 3D design to compensate for distortion introduced during the 3D printing process, giving users greater confidence that the part that comes out of the printer will match the design on the screen.
There are many great additions to Netfabb 2018 beyond the improvements described here, so do go check them out at Autodesk.com. The Autodesk Generative Design technology will be available to current and future Netfabb Ultimate 2018 users later this year.
I want to say a big thank you to our research partners who built this technology from the ground up and turned it into what it is today. I also want to thank everyone one across the Netfabb team for their excitement and hard work. I know a lot of our customers have been anxiously awaiting this technology and it’s great to see it finally come to fruition!
Pingback: It’s here! Generative design technology makes its commercial debut in Fusion 360 Ultimate - Manufacturing Lounge
Pingback: Generative design makes its commercial debut in Autodesk Fusion 360 Ultimate
Pingback: Artificial intelligence applications in additive manufacturing (3D printing)
Pingback: Autodesk’s Generative Design tools to be built into NetFabb - TECHRELEASE
Pingback: Why I may need to rethink Artificial Thinking - Wilde Analysis Ltd : Engineering simulation, safety & reliability, and design & optimisation
Pingback: Con Netfabb e Fusion 360 Ultimate anche Autodesk Generative Design – EUROLAMEC NEWS Meccanica e Tecnologia
Pingback: Autodesk Expands Autodesk Generative Design Tech Preview - Manufacturing Lounge