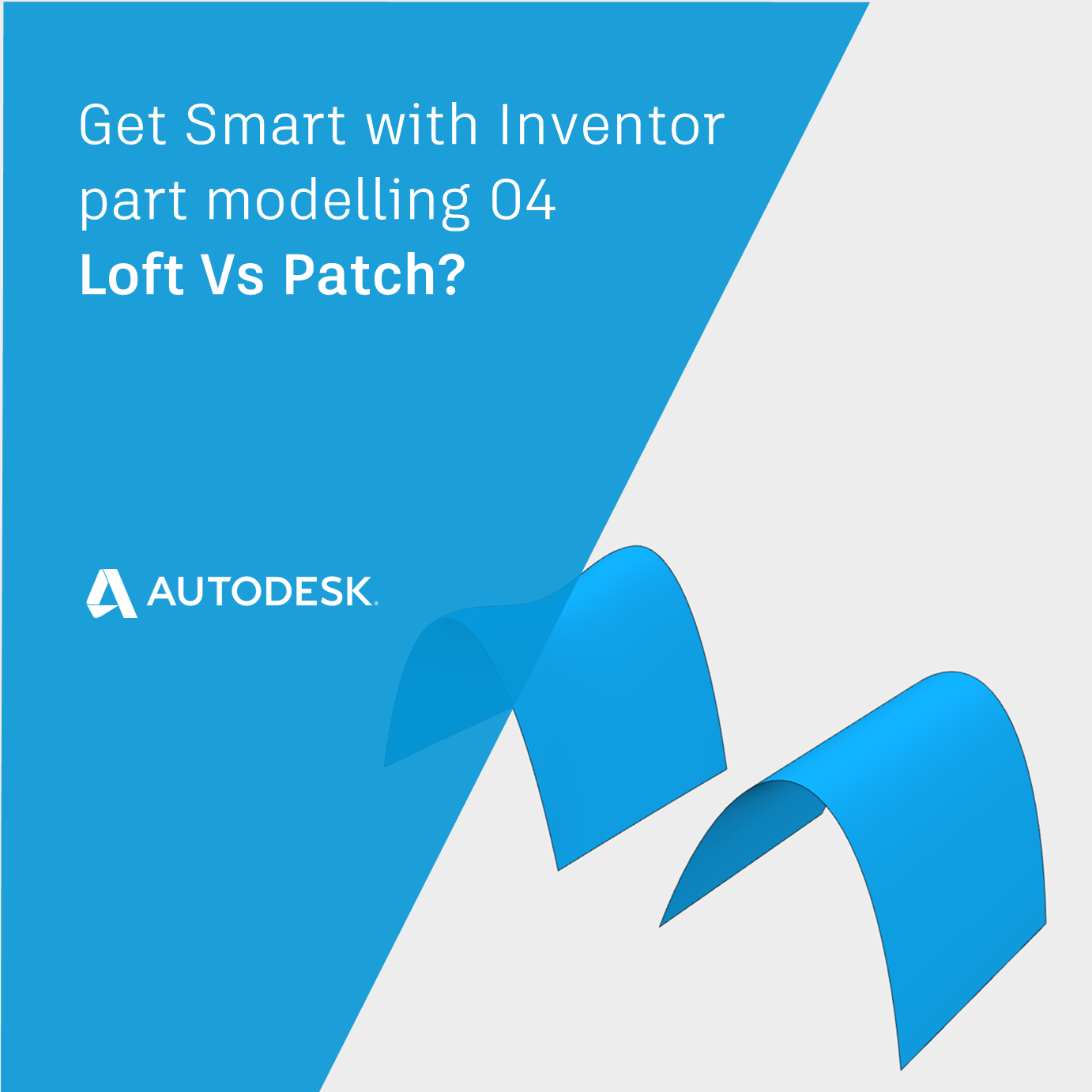
In this post we’ll learn what the difference is between a loft verses patch, and how we can use that knowledge.
What is a Loft really?
When we ask Autodesk Inventor to ask ASM to generate a shape using the Loft command, ASM will create a four-sided surface, which it will then ‘fit’ to the geometry we have provided.
For this reason, Loft works well when creating four sided surfaces. Loft also works pretty well when creating surfaces which have more than four edges, but in this case, Loft will just divide the shape up into four side surfaces for us.
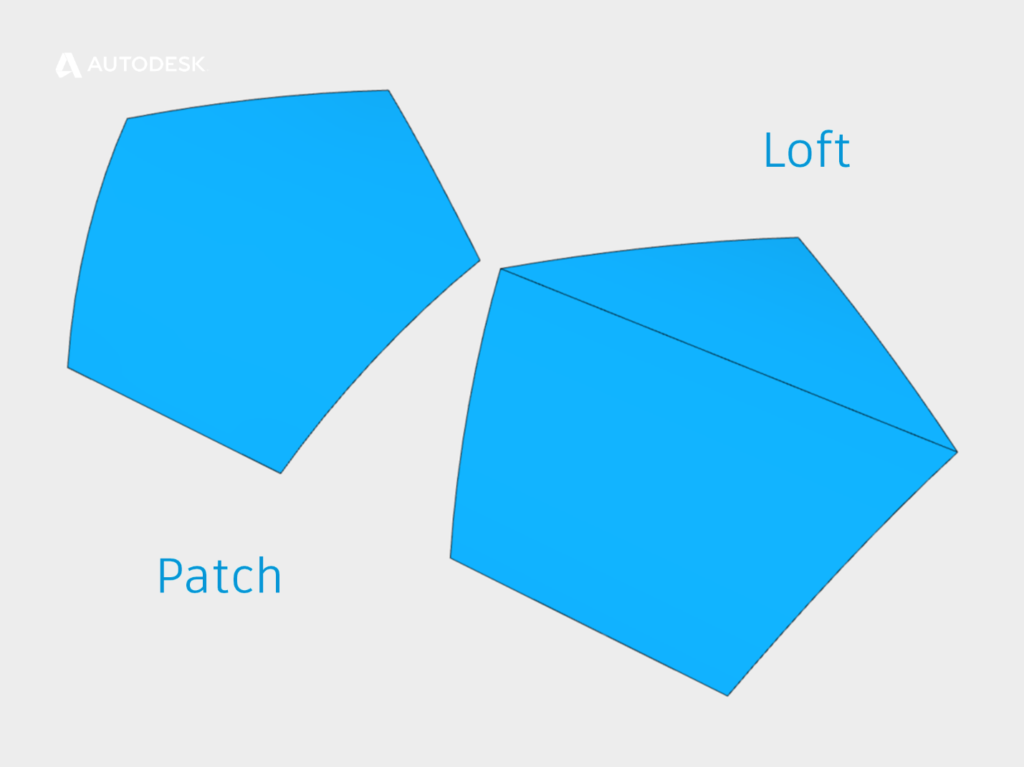
Loft Vs Patch for a five sided shape
So what is a Patch?
The Patch tool also allows us to create surfaces from multiple profiles. The patch tool also can ‘Warp’, allowing us to set curvature continuity on its boundaries (Click here to read post 01 in the series for a definition of Curvature continuity).
A Patch is also a four-sided shape, but instead of FITTING the patch to its inputs, ASM will TRIM the patch surface to the inputs.
When should I use Loft instead of Patch?
Loft is great for covering large areas. Loft creates a ‘Ruled surface’, which means that the shape goes directly from one profile to another without any dips.
When should I use Patch instead of Loft?
A Patch is best used for surfacing a non-four side edge chain. The Patch tool is the only tool which will fill a single entity shape (a circle!).
The Patch tool has an excellent ‘Tolerance’ feature, meaning that the edge chains don’t have to join perfectly at the corners for the Patch tool to return a result.
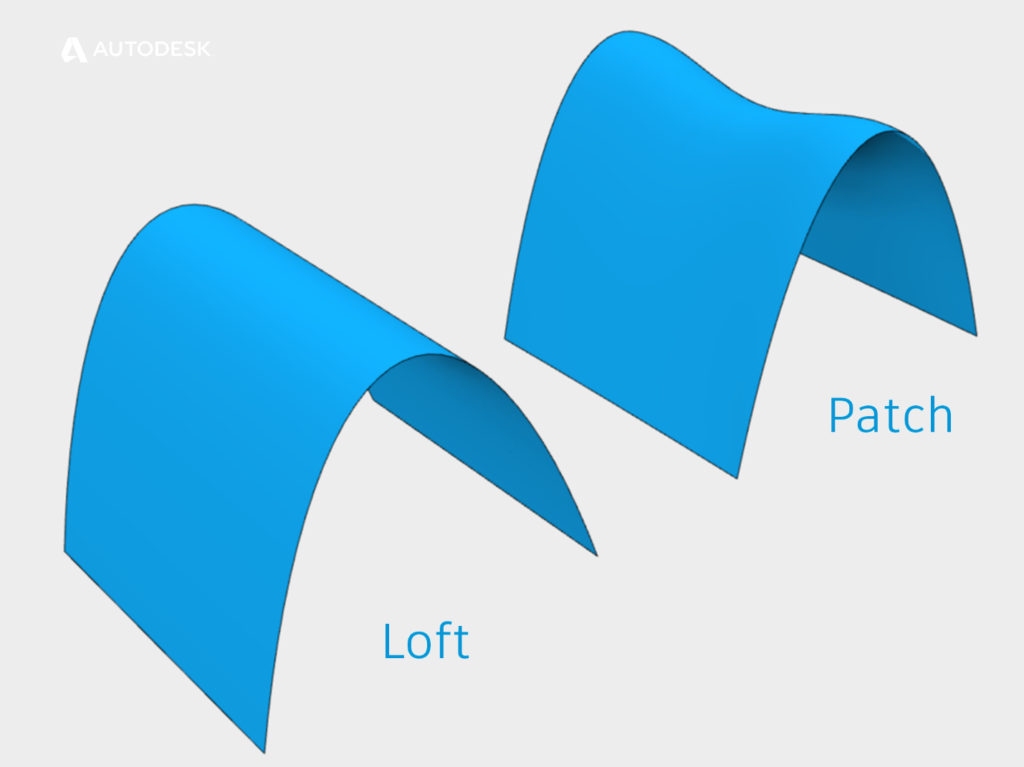
Loft Vs patch surfaces
Filleting best practice | Get Smart with Inventor Part Modelling 05
This blog post is based on an Autodesk University class, originally by Jake Fowler and later updated by Inderjeet Wilkhu and Paul Munford. You can watch a recording of the class, and download a handout that goes with this presentation from the Autodesk University website here:
Autodesk University Online: The Inventor 7 Deadly Sins of 3D Part Modeling