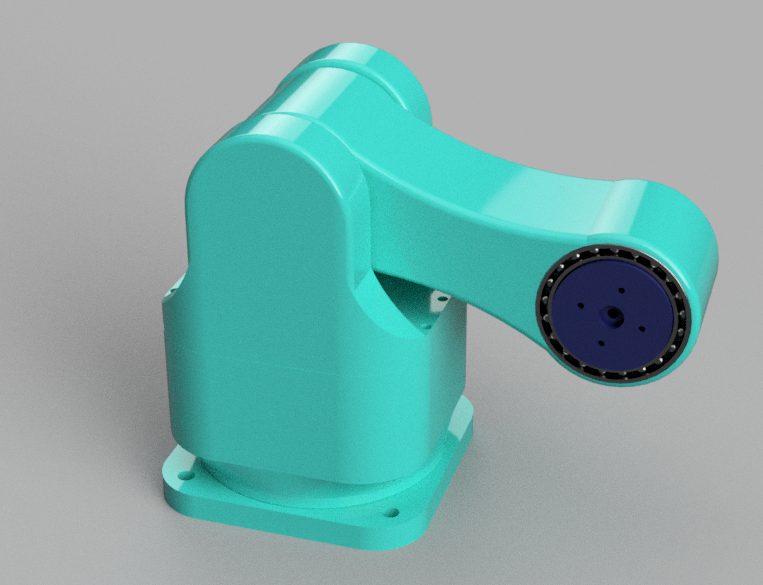
College student Nachum Twersky and high school student Teddy Warner participated in the New Year, New Skill Student Design Challenge, taking the grand prize and second place wins, respectively. Read on as they share insights into the wonderful world of upskilling by using Instructables as a platform to prepare for their future careers.
Twersky is a Mechanical Engineering student transferring to Columbia University in the fall to focus on mechanical systems and robotics. Warner, a senior high school student in the fall at Charlotte Latin High School, is hoping to study computer or electrical engineering in college.
How did you first get interested in design and engineering?
Twersky: I’ve always been interested in building and creating. As a kid, I was very into Legos and K’nex and always tried to find ways to deviate from the given instructions to make my own monstrosities. Growing up, I didn’t have too many opportunities to learn about design and engineering, but I did have a physics teacher in high school who was a retired mechanical engineer. He made physics fun. I can credit him with my first introduction to mechanical engineering.
Warner: I’ve been driven to make for as long as I can remember, but my elementary school STEM teacher, Mrs. Pritchard, did leave a big impact on me and my passion for engineering. Mrs. Pritchard, a vested STEM enthusiast, ran a robotics club for the older elementary school students. She always encouraged us to learn by doing and allowed us to experiment with our own ideas while teaching workflows & basic tools. Fast forward a few years to 2017 when I got my first 3D printer as a 7th grader. This is where I dove head-first into the world of fabrication. I used Tinkercad as a means of creating my own printable models & existing 3D meshes and have since transitioned over to Autodesk Fusion 360.
What keeps you inspired on your journey as CAD designers?
Twersky: I only got into design in the last couple of years when I discovered my college had a makerspace hidden in the deep recesses of the library. To start 3D printing, I needed to be able to design what I wanted to print. So, I started with Tinkercad and immediately moved to Fusion 360 for more complex designs and measurements.
Warner: My CAD projects often combine a variety of digital fabrication tools and techniques. Through direct experience in these projects, I gain most of my knowledge and inspiration. My lab teaches Fusion 360 in its freshman and sophomore engineering, and it has become a crucial tool for our digital fabrication workflow. By participating in projects like these, I notice I’ve grown more prepared and inspired to work in this industry.
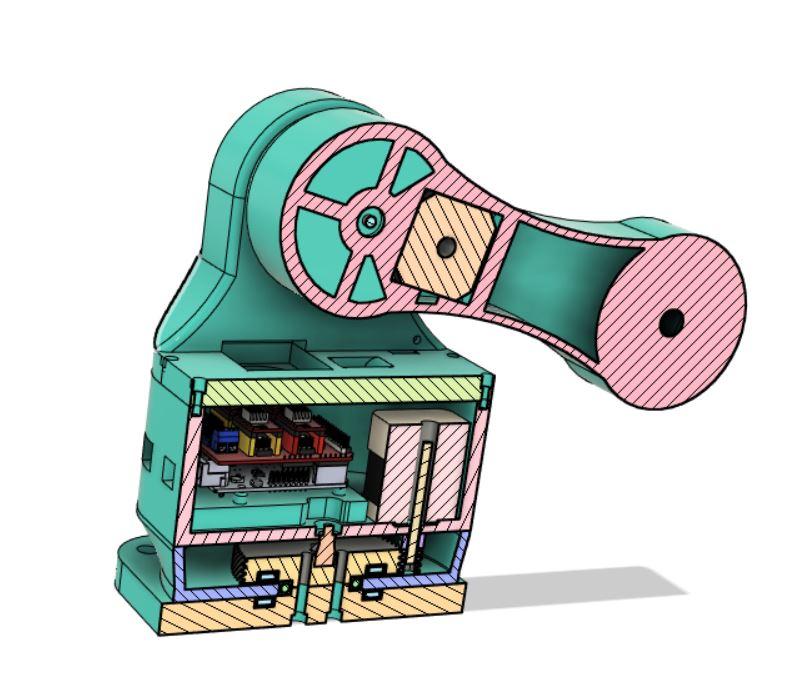
What inspired you to participate in the New Year, New Skill challenge?
Twersky: I love the Instructables website. It’s a genius idea for a website where people can share their ideas and projects. I’ve been visiting Instructables for years and have always browsed the contest sections to see what other people can come up with to fulfill the contest requirements. I came across the New Year, New Skill contest in my weekly browse of Instructables and thought it would be a great way to hone my design skills. Check out my winning design here.
Warner: The student design challenge caught my eye, especially since I’ve been wanting to expand the reach of my published projects on Instructables. This challenge allowed me to gain more traction on the site. Soon after the Parametric Bottle Cap Generator design was published, the project was featured on the site and has now accumulated nearly six thousand views! Check out some of my other designs on my Instagram.
What worked well in your design process?
Twersky: I’ve been using Fusion 360 for over 3 years and love the simplicity of the software. I was inspired by a YouTuber to make a robotic arm that holds a heavy DSLR camera for videos. I was excited about the gear mechanism since I’d never heard of a strain wave gear before. It was the first thing I tried to design for this arm and it involved a ton of prototyping. This is where Fusion 360 really shined. It made changing parameters a breeze, whether through the parameter settings or by going back in the timeline to change a small measurement. With Fusion 360, I was able to make around 16 prototypes, all with different motors, different bearings, and different 3D printed materials.
Warner: The design work behind my Parametric Bottle Cap Generator honestly went rather smoothly. I stayed in Fusion 360’s Design workspace for this model, using an array of tools to build the generator such as Fusion’s Change Parameters, Sketch, Mirror, Coil, Extrude, Fillet, Chamfer & Loft tools. Fusion 360’s streamlined parametric design tools enabled rapid prototyping on my Parametric Bottle Cap Generator. This feature of the software was the real backbone to my Parametric Bottle Cap Generator. The streamlining of such a powerful tool allows Fusion 360 to work as an aspect of my project, rather than the project itself. I really appreciate the ability to go from an envisioned idea into the research & planning behind a project and then quickly to a mock-up as a final product.
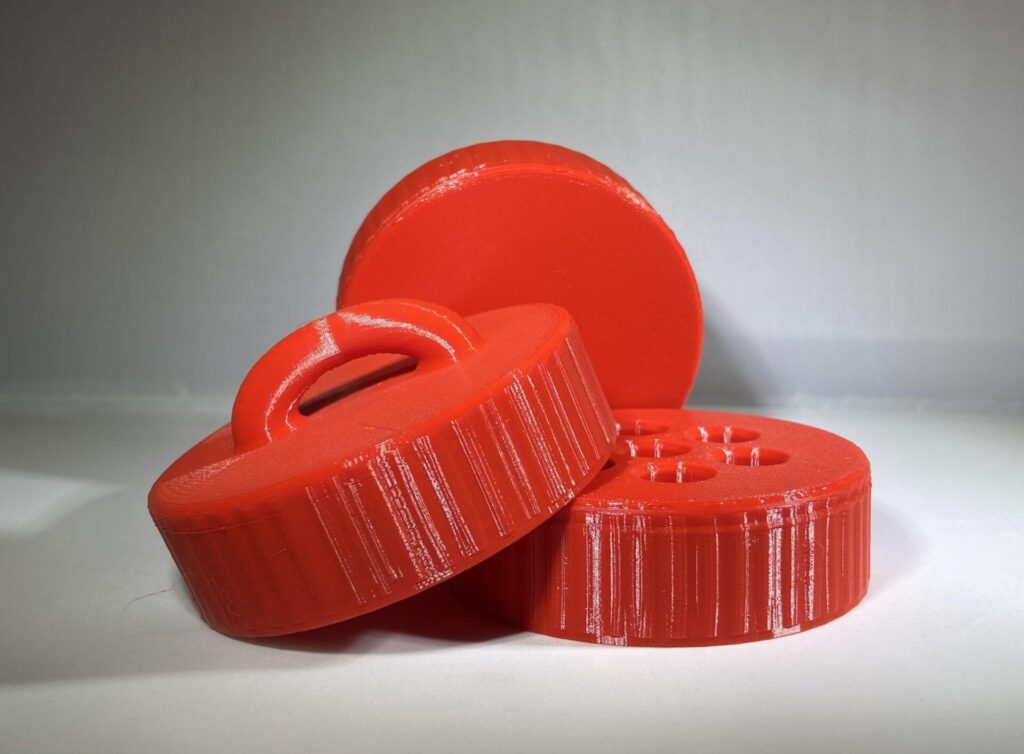
How do you feel experiences like this one will prepare you for your future career?
Twersky: This experience taught me how to get creative and finish a project from conception to design. We know that no design is going to work on the first try. However, not many people are prepared for the frustration that comes with something not working on the 15th try. Those moments where I just wanted to throw everything against the wall were extremely important to push through early on and I imagine this resilience will help me in my future career.
Warner: My experience in the student design challenge validates how much I love designing and pushes me to continue working on my passion. I hope to use the skills I’ve gained in whatever future career I find myself in.